Continue reading “Fully Portable Equipment Storage Building”
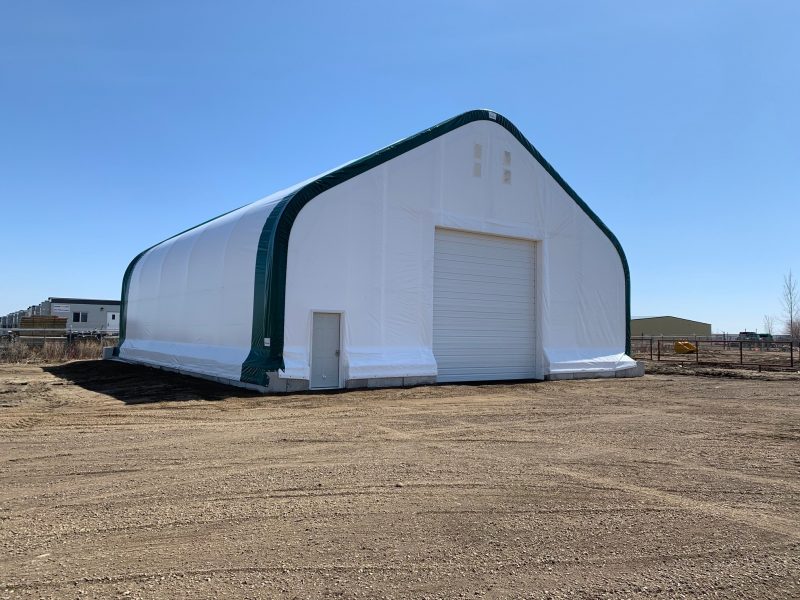
🇨🇦 Proudly Canadian 🇨🇦 |
Continue reading “Fully Portable Equipment Storage Building” →
Reducing maintenance and utility costs associated with your storage buildings is a smart way to improve the operational efficiency of your business operations. Making a smart purchase decision includes not only taking into account the upfront capital cost of the building but also the on-going operational costs of the building.
Setting aside the capital outlay for the building, there are a number savings that a FastCover fabric building will provide which may not be immediately obvious. The first is the time and expense saved to erect the building. Because the building is shipped in modular components, on-site construction time is drastically reduced where buildings can be completed sometimes in days as compared to weeks or months with buildings which must be completely constructed on-site. This also means your building is finished and ready for use in your business sooner.
Now consider the post-construction state of your building, as this is expected to last for many years. You will have recurring monthly expenses for utilities and maintenance on any style of building. A FastCover fabric building can help to reduce a number of monthly expenses due to the nature of the materials used to manufacture the building. The most obvious difference between a fabric building and steel or wood construction building is the use of a fabric cover. This fabric cover offers numerous advantages. The first is that it allows a tremendous amount of natural daylight to pass through the cover to the building’s interior, virtually eliminating the need for daytime artificial lighting. Even on cloudy days, there is often ample light to perform most activities inside the building without flicking on the light switch and having the power meter spinning. In early morning hours and nighttime when we no longer have the free benefit of the suns light, artificial lights can be used more efficiently as the bright white underside of the cover reflects and disperses light so that typically fewer light fixtures are needed.
Unlike a metal roofed building often used for storage buildings, a fabric building cover will not radiate the heat and cold of the extreme weather conditions we experience. Combine this with a cover that is effectively a one-piece sealed membrane and there will be substantially less air through cracks and perforations traditional buildings tend to have.
Some building styles require that the roofing and siding materials such as roof tar or shingles and exterior wall paint must be frequently maintained or replaced on a periodic basis. With a FastCover fabric building chosen for your storage building, there is no need to paint or shingle the roof and walls. The covers should be checked for tension periodically but are otherwise virtually self maintaining. Dirt and dust have a difficult time adhering to the polyethylene fabric and normally wind and rain are enough to blow off or wash off any that does manage to sit on the covers.
The building’s steel superstructure is post-weld powder-coat painted in our own paint booth. The extremely smooth finish helps to prevent cover wear and protects the steel framework from rust and corrosion.
One cost saving factor that few other storage buildings can match is the ability to take your investment with you if your business circumstance result in a move of locations. A FastCover building is designed with an exclusive continuous base rail frame system which affords it a tremendous range of options in regards to foundations. So flexible are these options that the foundation itself may be temporary and if the need arises, a FastCover storage building can be disassembled, building and foundation moved, and re-erected at the new site.
Note: link to this article from commercial equipment storage
Our Client purchased a significant number FastCover Fabric Structures for various locations to store salt, sand and large snow clearing equipment for the Province of Alberta, Canada. Working with the Client, it was determined that the size of buildings would range from 30 feet to 72 feet wide and up to 230 feet in length.
The structures for storage of sand and salt were completely epoxy coated which provides tremendous extended life to steel in facilities that are prone to high corrosion. Although epoxy coating adds initial cost to FastCover Structures, that incremental cost is minute compared to cost to replace any steel components due to premature corrosion. With Safety being paramount to our Client, epoxy coating ensured the Client was confident in the durability of the engineered structures.
The Equipment storage buildings required a completely different specification. The Client required an enclosed storage area to thaw equipment during down time, allowing them to keep equipment clean, reduce the opportunity for rust, all while providing an environment where maintenance and repairs can be done on their equipment. Each FastCover Fabric Structure was lined with an interior insulator to create a barrier resulting in reduced heat loss. This enabled the Client to install radiant heaters making the structure usable for maintenance and repair. These structures are also fully electrified allowing for the use of power tools and plugging in snow clearing equipment which ultimately extends their life.
FastCover fabric buildings were the ideal solution for this customer to install several buildings efficiently with the option of them being moved and/or quickly taken down on a temporary site compared to traditional buildings.
Another successful FastCover project. For more information on how FastCover can assist with your project please contact us online or call 1-866-657-7172